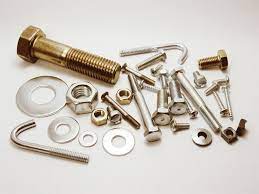
In life, bolts, nuts, screws, etc. are often mentioned. So what is the difference between the fasteners? Let me explain the 12 types of fasteners for you as below.
1. Bolt
Bolts are widely used in detachable connections in mechanical manufacturing. It is generally used in conjunction with a nut (usually plus a washer or two washers).
A) General purpose bolts
There are many varieties, including hexagon heads and square heads. Hexagon head bolts are the most common applications and are classified into product grades. Such as A, B, and C according to manufacturing accuracy and product quality. The A and B grades have the most applications. They are mainly used in the important, high-precision assembly, and places subject to large shocks, vibrations, or variable loads.
Hexagon head bolts can be divided into two types: Hexagon head and large hexagon head according to the size of the head supporting area and the size of the installation position. Types with holes in the head or screw are used when locking is required. The square head of the square head bolt has a larger size and a force-receiving surface. It is convenient for the wrench mouth to be stuck or against other parts to prevent rotation. It is often used on rough structures. And sometimes used in T-slots to facilitate the loosening of bolts in the grooves to adjust the position.
B) Bolts for reaming holes
When using, insert the bolts tightly into the reaming holes to prevent dislocation of the workpiece.
C) Anti-rotation bolt
There are square neck and tenon.
D) Special purpose bolts
including T-slot bolts, joint bolts and anchor bolts. T-slot bolts are mostly used in places that need to be disconnected frequently. Anchor bolts are used to fix the frame or motor base in the cement foundation.
E) High-strength bolt connection pair for steel structure
Generally used for friction-type connection of steel structures such as buildings, bridges, towers, pipeline supports, and hoisting machinery.
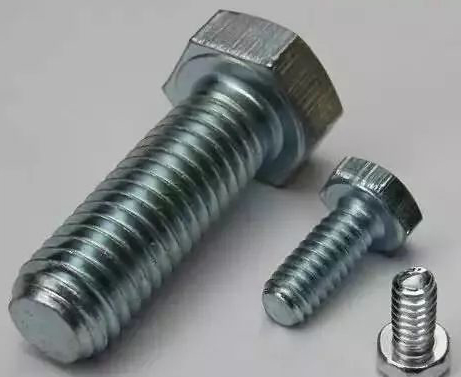
2. Nut
A) General purpose nuts
There are many varieties, including hexagonal nuts, square nuts and so on. Hex nuts are most commonly used with hexagon bolts. According to the manufacturing accuracy and product quality, it is divided into product grades such as A, B, and C. Hexagon thin nuts are used as auxiliary nuts in the anti-loosening device, which can be used for locking, or where the threaded connection pair is mainly subjected to shearing force. Hexagon thick nuts are mostly used in connections that are often disassembled. The square nut is matched with the square head bolt, the wrench is stuck and not easy to slip, and it is mostly used for rough and simple structures.
B) Slotted nut
Mainly refers to the hexagonal slotted nut, that is, the slot is machined on the hexagonal nut. It is used in conjunction with a bolt with a hole in the screw and a split pin to prevent the bolt from rotating relative to the nut.
C) Locking nut
Refers to the nut with locking function. There are nylon insert hexagonal lock nuts and all-metal hexagonal lock nuts. The hexagonal nylon ring lock nut has a very reliable anti-loosening ability. It has the advantages of not damaging the bolts and connected parts and being able to be frequently installed and unloaded under the operating temperature of -60~+100℃ and certain medium conditions.
D) Special purpose nuts
Such as wing nuts, cap nuts, knurled nuts, and embedded nuts. Wingnuts can generally be disassembled without tools, and are usually used in places that need to be disassembled frequently and are not stressed. Cap nuts are used where the end screws need to be covered.
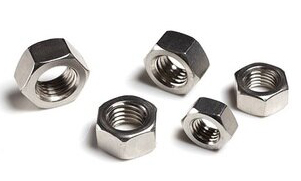
3. Screw
Screws are usually used alone (sometimes with washers). Generally used for tightening or tightening, it should be screwed into the internal thread of the body.
A) Machine screws
There are many varieties due to different head and groove shapes. There are several types of head types: cylindrical head, pan head, countersunk head and half countersunk head. The head grooves are generally slotted (slotted), cross grooves and hexagonal inner grooves. The cross recessed screw has good neutrality when screwing, and the head strength is greater than that of the slotted type, and it is not easy to be bald. Generally, it is mostly used in mass production. Hexagon socket screws and hex socket screws can apply a larger tightening torque, and the connection strength is high. The head can be embedded in the body, and it is used for the connection where compact structure and smooth appearance are required.
B) Set screws
Set screws are used to fix the relative position of the parts. The head has a slot, hexagon socket and square head. The square head can apply a larger tightening torque, the tightening force is large, and it is not easy to be bald, but the size of the head is large, it is inconvenient to be buried in the parts, and it is unsafe, especially the moving parts. The slotted and hexagonal ones are easy to sink into the parts. The end of the set screw varies according to the requirements of use.
Generally, the most commonly used three types are cone end, flat end and cylindrical end. The tapered end is suitable for parts with low hardness. When using a non-pointed taper-end screw, a hole should be punched on the top tight surface of the part, and the taper surface is pressed against the edge of the hole. The end is a flat-end screw, which has a large contact area and does not damage the surface of the part after being tightened. It is used for tightening a flat surface with a large hardness or where the position is frequently adjusted. The cylindrical end screw does not damage the surface of the part. It is mostly used to fix the parts mounted on the pipe shaft (thin-walled part). The cylindrical end is pushed into the hole on the shaft. The round end is resistant to shear and can transmit larger loads.
C) Hexagon socket screws
Hexagon socket screws are suitable for occasions where the installation space is small or the head of the screw needs to be buried.
D) Screws for special purposes
such as positioning screws, non-stripping screws and eyebolts.
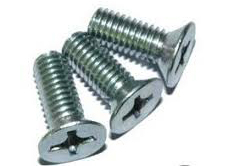
4. Stud
Studs are mostly used to connect one of the connected parts with a large thickness. Its need to be used where the structure is compact or the bolt connection is not suitable for frequent disassembly. Studs are generally threaded at both ends (single-end studs are threaded at one end). Usually, one thread is firmly screwed into the body of the component. And the other end is matched with the nut to play the role of connection and fastening. But to a large extent it also has a fixed distance function.
A) Unequal length double-ended studs
Suitable for occasions where one end is screwed into the body of the component for connection or fastening.
B) Equal-length double-ended stud
Suitable for connecting or fixing the distance between the two ends and the nut.
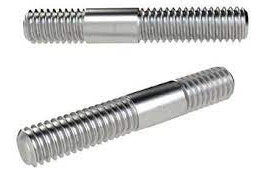
5. Wood screws
Wood screws are used to screw into wood to connect or fasten.
It is divided into many varieties due to different head and trough types. There are several types of head types, such as round head, countersunk head, and semi-sunk head. There are two types of head grooves: slotted (one-shaped groove) and cross groove.
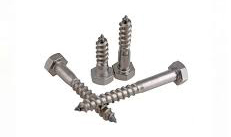
6. Tapping screw
The working screw hole matched with the self-tapping screw does not need to be tapped in advance, and the internal thread is formed while the self-tapping screw is screwed in.
A) Ordinary self-tapping screws
The thread conforms to GB5280, with a large pitch, suitable for use on thin steel plates or copper, aluminum, and plastics.
B) Self-tapping locking screw
The thread conforms to the ordinary metric coarse thread. Suitable for use in occasions requiring vibration resistance.
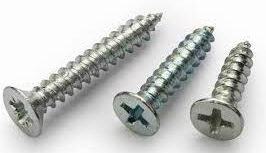
7. Washer
Anti-loosening washer
The washer is placed between the supporting surface of bolts, screws, nuts, etc. and the supporting surface of the workpiece to prevent loosening and reduce the stress on the supporting surface.
A) Flat washers
Used to overcome the unevenness of the supporting surface of the workpiece and increase the stress area of the supporting surface.
B) Spring (elastic) washers
Spring washers rely on elasticity and oblique friction to prevent loosening of fasteners. Widely used in connections that are frequently disassembled. The inner tooth elastic washer and the outer tooth elastic washer have many sharp elastic warped teeth on the circumference. It can be pressed against the supporting surface to prevent the loosening of the fastener. Internal tooth elastic washers are used under the heads of screws with smaller head sizes. External tooth elastic washers are mostly used under bolt heads and nuts. Toothed elastic washers are smaller than ordinary spring washers, and the fasteners are evenly stressed and reliable in preventing loosening, but they are not suitable for frequent disassembly.
C) Non-return washers
There are internal teeth lock washers, external teeth lock washers, single-ear lock washers, double-ear lock washers, and stop washers for round nuts. Single-ear and double-ear stop washers allow the nut to be tightened at any position to lock it, but the fasteners should be close to the edge.
D) Inclined washers
In order to adapt to the inclination of the working bearing surface, oblique washers can be used. The oblique washer is used to level the inclined surfaces such as channel steel and I-steel flanges so that the nut supporting surface is perpendicular to the nail rod to avoid bending force on the screw rod when the nut is tightened.
Lock washer
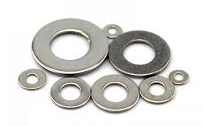
8. Shaft collar
The shaft collar is mainly used to position, lock or stop the parts on the shaft or in the hole.
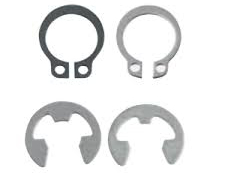
A) Circlips
The elastic circlips for shaft and hole are clamped in the shaft groove or hole groove for the rolling bearing to stop after being installed. In addition, there is an open retaining ring for the shaft, which is mainly used for positioning the parts in the shaft groove but cannot bear the axial force.
B) Wire shaft collar
Wire shaft collar and wire locking ring for holes (for shafts). The wire shaft collar is installed in the shaft groove or the hole groove for the positioning of the parts and can also bear a certain axial force.
C) Locking shaft collar for shaft parts
Shaft collar locked with taper pin and shaft collar locked with screw. Mainly used to prevent axial movement of parts on the shaft.
D) Shaft end shaft collar
Shaft end shaft collar fastened with screws and shaft end shaft collar fastened with bolts. Mainly used to lock the parts fixed on the shaft end.
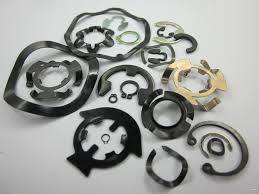
9. Pin
Pins are usually used for positioning, can also be used to connect or lock parts, and can also be used as overload shearing elements in safety devices.
A) Cylindrical pins
Cylindrical pins are mostly used for fixing parts on shafts, transmitting power, or as positioning elements. Cylindrical pins have different diameter tolerances, which can be used for different matching requirements. Cylindrical pins are generally fixed in the hole by interference, so it is not suitable to disassemble more.
B) Taper pin
The taper pin has a taper of 1:50, which is easy to install and can also ensure self-locking. It is generally used as a positioning element and a connecting element and is mostly used in places that require frequent disassembly. Internally threaded taper pins and threaded taper pins are used in holes that do not pass through or in holes where it is difficult to punch a pin. The end of the open-end tapered pin can be opened after being driven into the hole to prevent the pin itself from slipping out of the hole.
The pin holes of cylindrical pins and various tapered pins generally need to be reamed. After multiple assembly and disassembly, the accuracy of positioning and the fastening of the connection will be reduced, and only a small load can be transmitted. The elastic cylindrical pin itself has elasticity, is installed in the hole to maintain tension, is not easy to loose, and is convenient to disassemble, and does not affect the matching properties, and the pin hole does not need to be hinged. Hole pins and pin shafts are used for hinge joints.
C) Split pin
Split pin is an anti-loosening device for connecting parts. When in use, it is inserted into the pin holes of nuts, bolts with pin holes or other connecting parts, and then the feet are separated.
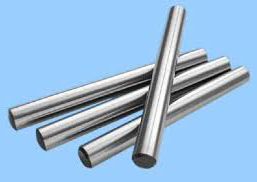
10. Rivet
The rivet has a head at one end, and the shank has no thread. When in use, the rod is inserted into the hole of the connected piece, and then the end of the rod is riveted to play the role of connection or fastening.
A) Hot-forged rivets
Generally, they have larger specifications and are mostly used in locomotives, ships, boilers, etc. The heads are usually formed by hot forging.
B) Cold heading forming rivets
The general diameter is 16mm, and the head is usually formed by cold heading.
C) Hollow and semi-hollow rivets
Hollow rivets are used in places where the shear force is not large, and are often used to connect non-metallic parts such as plastic, leather, wood, and canvas.
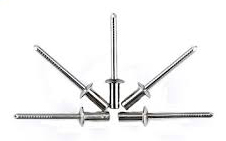
11. Connecting pair
The connection pair is a combination of screws or bolts or self-tapping screws and washers. After the washer is installed on the screw, it must be able to rotate freely on the screw (or bolt) without falling off. It is mainly used for tightening or tightening.
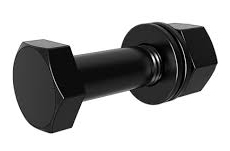
12. Others
Mainly include welding nails and so on.
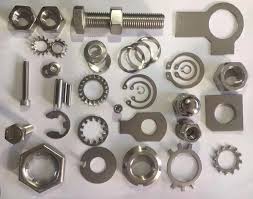
Selection principle of variety
① Considering the efficiency of processing and assembly, the variety of fasteners should be minimized in the same machine or project.
② From economic considerations, commodity fastener varieties should be preferred.
③ According to the expected use requirements of fasteners, determine the selection of varieties in terms of type, mechanical properties, precision and thread.
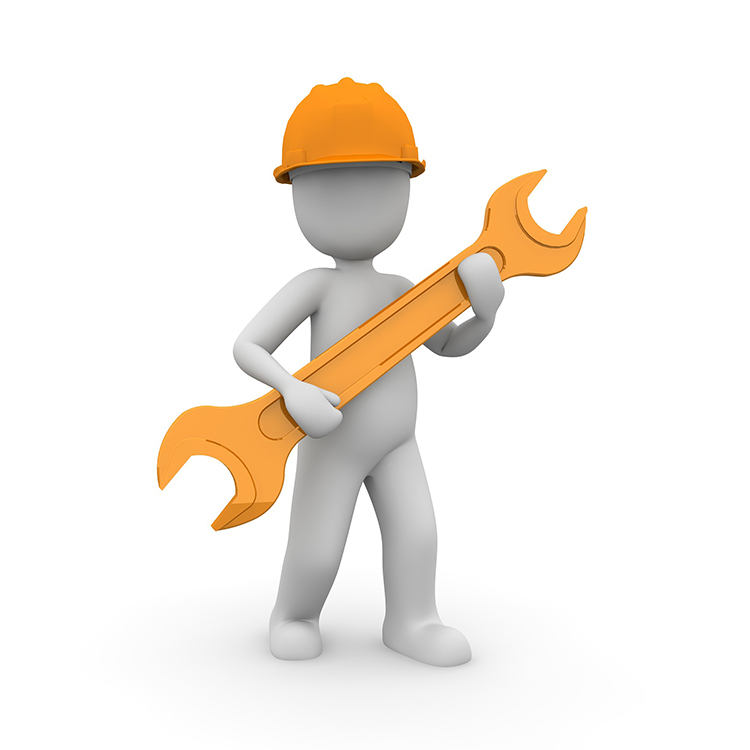