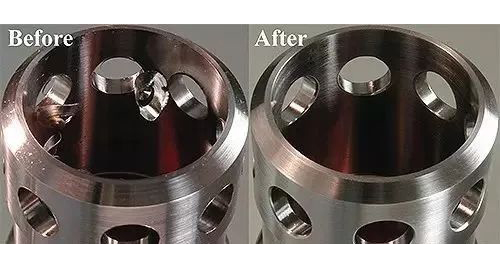
Burrs are everywhere in the metalworking process. No matter how advanced the precision equipment you use, it will be born along with the product. It is mainly a plastic deformation of the material that generates an excess of iron filings at the edge of the material being machined. Especially ductile or tough materials are particularly prone to burrs. So It needs to use some deburring methods to remove burrs.
The main types of burrs are flying edge burrs, sharp corner burrs, splashes, and other prominent excess metal residues that do not meet the requirements of the product design. For this problem, there is no effective method so far to eliminate it in the production process. Therefore, in order to ensure the product design requirements, engineers have to work on post-process removal. So far, there are many different methods and equipment for removing burrs different products.

In general, deburring methods can be divided into four main categories.
1. Coarse grade (hard contact)
In this category, there are cutting, grinding, filing and scraper processing.
2. General grade (soft contact)
Those belonging to this category include belt grinding, lapping, elastic grinding wheel grinding and polishing.
3. Precision grade (flexible contact)
Precision grade (flexible contact)
4. Ultra-precision grade (precision contact)
In this category are abrasive flow deburring, magnetic abrasive deburring, electrolytic deburring, thermal deburring and dense radium powerful ultrasonic deburring, etc. These deburring methods can obtain sufficient part machining accuracy.
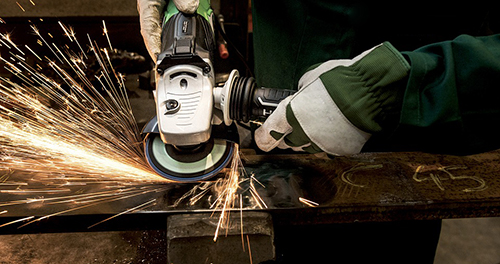
The 10 most common deburring methods have been compiled for you as below
1) Manual deburring
This is also a method commonly used by general enterprises. Use files, sandpaper, grinding heads, etc. as auxiliary tools. The file has manual file and pneumatic displacement.
Brief comment: The labor cost is more expensive, the efficiency is not very high, and it is difficult to remove the complicated cross holes. The technical requirements for workers are not very high, and it is suitable for products with small burrs and simple product structure.
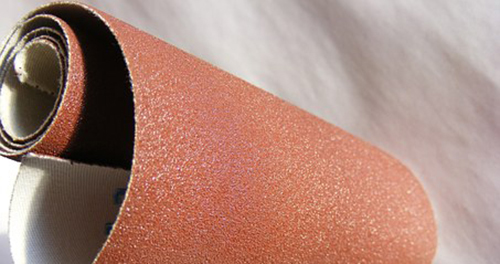
2) Die deburring
Removing burrs is carried out with a punching die and a punching machine.
Brief comment: A certain amount of punching die (rough die + fine die) production cost is required. It may be necessary to make a shaping die as well. It is suitable for products with simple parting surface, and the efficiency and deburring effect is better than manual.
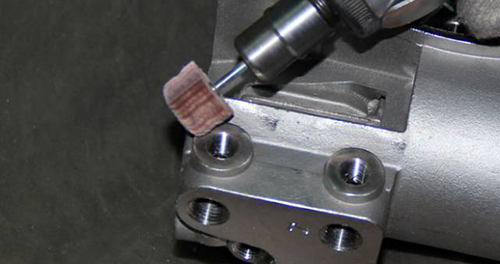
3) Grinding and deburring
This type of removing burr contains vibration, sandblasting, roller and other methods, and is currently used by more companies.
Brief comment: There is a problem that the removal is not very clean. May need to follow up manual processing residual burrs or with other ways to deburr. Suitable for small products with large batches.
4) Frozen deburring
Using the cooling temperature to make the burr quickly brittle, and then spraying projectiles to remove the burr.
Brief comment: The price of the equipment is a little expensive. It is suitable for products with small burr wall thickness and small products.
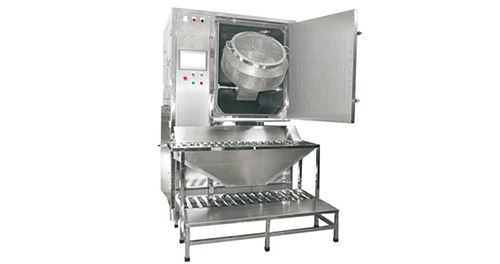
5) Thermal explosion deburring
It is also called thermal deburr and explosion deburr. By passing some flammable gas into an equipment furnace, and then through the action of some media and conditions, the gas instantly explodes, and the energy generated by the explosion is used to dissolve and remove burrs.
Brief comment: The equipment is very expensive, the operation technology requires high, the efficiency is low, and the side effects (rust, deformation). Mainly used in some high-precision parts and components, such as precision parts such as automotive and aerospace.
6) Deburring of engraving machine
Brief comment: The price of the equipment is not very expensive. It is suitable for simple space structure and simple and regular deburring position.
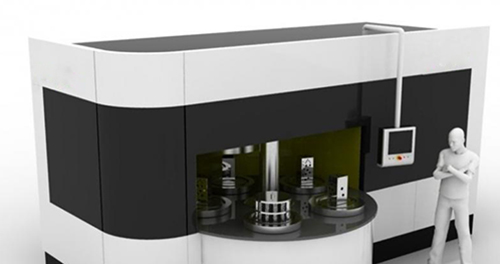
7) Chemical deburring
Using the principle of electrochemical reaction, the deburring operation of parts made of metal materials is automatically and selectively completed.
Brief comment: Suitable for internal burrs that are difficult to remove. Suitable for small burrs (thickness less than 7 filaments) in pump bodies, valve bodies and other products.
8) Electrolytic deburring
An electrolytic machining method that uses electrolysis to remove burrs on metal parts.
Brief comment: The electrolyte is corrosive, and the parts near the burrs are also subjected to electrolysis. The surface will lose its original luster and even affect the dimensional accuracy. After deburring, the workpiece should be cleaned and anti-rust treatment. Electrolytic deburr is suitable for removing burrs from cross holes in hidden parts or parts with complex shapes. The production efficiency is high, and the deburring time generally only takes a few seconds to tens of seconds. It is suitable for deburring of gears, connecting rods, valve bodies and crankshaft oil passages, as well as rounding of sharp corners, etc.
9) High-pressure water jet deburring
Using water as a medium, use its instant impact to remove burrs and flashes generated after processing, and at the same time achieve the purpose of cleaning.
Brief comment: The equipment is expensive, mainly used in the heart of the car and the hydraulic control system of the construction machinery.
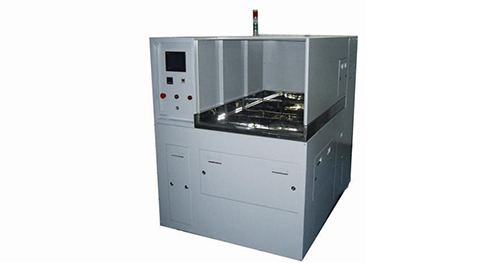
10) Ultrasonic deburring
Ultrasonic waves generate instantaneous high pressure to remove burrs.
Brief comment: mainly for some micro glitches. Generally, if the burrs need to be observed with a microscope, you can try to remove them by ultrasonic method.

What other methods of burr removal do you know? Leave a comment below and let’s share and discuss.
If you like this post, please support us and help to share it, thanks in advanced.